- Es fácil que un ducto supere los 1.000 mts o incluso más, hay instalaciones que por causa diversas pueden alcanzar lo 10.000/15.000 mts
- Para disminuir la longitud es necesario pendientes muy fuertes (dificultad de acceso y montaje, incluso con medios aéreos)
- Como hemos visto es la causa de mayores perdidas de cabeza.
- PERO nos queda un "punto negro", que es el riesgo frente al golpe de ariete (tanto positivo; cierre, como negativo; apertura)
Este fenómeno, golpe de ariete, esta estudiado, documentado e informatizado hasta la saciedad, estos estudios los inicio Allievi a principio del siglo pasado a consecuencia de un gran desastre en un ducto. Aún así, hoy en día ocurren accidentes por esta causa.
Estos desastres suelen ocurrir por ignorancia, por reducir costes, etc. El golpe de ariete define unos ciertos parámetros, tales como:
- Espesor de del ducto.
- Volantes de inercia.
- Chimeneas de equilibrio.
- Tiempos de reacción.
Toda la formulación al respecto se puede encontrar en literatura de mecánica de fluidos, hidráulica, turbo máquinas hidráulicas, etc.; si las usas se prudente y que solo te sirvan para tener un ORDEN de GRANDEZA.
ACCIDENTE CLASICO Y REAL.
Se suelen producir en instalaciones antiguas que fueron diseñadas para trabajar con reguladores oleo-mecánicos (con tiempos de respuesta largos de 6 a 10 seg.) con materiales del ducto de bajas características mecánicas, (hierro colado o aceros de alto contenido en carbono), en comparación a las actuales y con sistemas de unión (roblones) y soldadura (a la llama) del momento de su instalación.
Actualmente para hacer frente a la demanda y maximizar ingresos y reducir consumo de caudales se trabaja en "horario de punta" y/o "disponibilidad inmediata".
Estos dos conceptos, "horario de punta" y " disponibilidad inmediata" exigen a las instalaciones puestas en cargas y desconexiones en tiempos muy cortos (del orden de 3 seg.). Esta aparente pequeña diferencia de tiempo de maniobra puede hacer pasar el tiempo de cierre de "lento" a "rápido" o a "instantaneo", cada uno de estos steeps puede mas que duplicar el "golpe de ariete"
Secuencia del incidente:
- Se realizan pruebas, no mas de 4 ó 5, de cierres rápidos, la instalación responde correctamente y se da el O.K. para disminuir los tiempos de maniobra.
- Pasado cierto tiempo, alguien se da cuenta que la potencia de la instalación a disminuido.
- Se llega a la conclusión que las tolerancias entre directrices y cierres es excesiva, que las directrices no ajustan entre ellas; por lo cual se decide realizar una reparación y si es necesario modificaciones para disminuir los caudales de fuga. Estas operaciones se realizan con las mejores técnicas y tolerancias alcanzables actualmente.
- Esta mejora (muy lógica) produce una disminución drástica de los caudales de fuga, es decir, ahora frente a un cierre del distribuidor todo el caudal sera "rechazado".
- No olvidemos que en algún momento o aprovechando la mejora se pudo sustituir el sistema oleo/mecánico por un sistema oleohidráulico con válvulas proporcionales o servo/válvulas, de respuesta muy rápida.
- El día de la nueva puesta en marcha, normalmente no ocurre nada, gracias a los coeficientes de seguridad y además otra vez en buena lógica solo se realizan 3 ó 4 pruebas.
- Al transcurrir del tiempo la tubería acaba fallando por agotamiento de sus características mecánicas (se supera el límite elástico del material) o por fatiga; además a todo ello debe sumarsele la perdida de espesor por corrosión a lo largo de la "vida util" del ducto.
Para evitar todo esto se debería realizar un análisis del espesor del ducto con ultrasonidos, verificar los materiales y sus características, simular la nueva situación y monitorizar los resultados en la puesta en marcha.
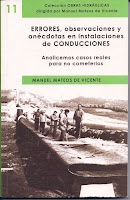
Continuará ...............................